Our 12-Step Repair process
We take great pride in our process. It allows us to ensure that your vehicle is repaired as quickly as possible, while closely monitoring repair quality and safety in every step along the path to getting your vehicle back on the road!
Step 1 Preliminary Inspection & Estimate
The first stage of repair is locating the initial impact and assessing the damaged area. This includes determining which components need to be replaced and which can be repaired. This process is either done by a body shop estimator or an insurance field damage appraiser. After this stage has been completed, an initial estimate, sometimes referred to as a “preliminary estimate,” is completed.
Step 2 Claim Handling Support
Once we have written an initial damage assessment, it is time to get the repairs scheduled. If your vehicle is safe to drive, we will find the soonest possible repair start date that fits your schedule and ours. During the time before your vehicle comes in for its scheduled date, we will work to get preliminary claim approval prior to ordering any parts or beginning any repairs. We work with the insurance companies and adjusters to provide preliminary estimates and high-quality photos to streamline the process.
Step 3 Check-in & Vehicle Drop-off
On your scheduled drop-off date, we will begin our check-in process. This includes your estimator reviewing the initial estimate and damage and obtaining repair authorization signatures so that we can work on your vehicle. Your estimator will then perform an inspection of your vehicle to note all damage areas associated with the current repairs as well as unrelated damage.
Step 4 Pre-Repair Wash & Scan
Once you have approved the repair work, we will begin the intake process on your vehicle. Your estimator will map the vehicle to identify all initial damage and repair notes. Then it will head to our detail department to be pre-washed. We do this to help identify all damage as well as remove road contaminants. We will then perform a pre-repair scan (if applicable) on your vehicle. This allows our technicians to identify what computer and safety systems your vehicle has as well as any DTCs or other issues that may be present and need to be addressed during the repair process.
Step 5 Disassembly & Inspection
Once we have completed a pre-repair diagnostic scan to identify any and all accident-related Diagnostic Trouble Codes (DTC’s) or system faults, we will begin the next stage of repair. This is when our technicians get to work completing a meticulous disassembly of the damaged area and thoroughly inspecting all damaged parts and body components. At this time, our technicians set up and measure the vehicle (if necessary) with our 3-D measuring systems to identify if there is any structural uni-body, frame, or related component damage that needs attention.
Step 6 Supplement Approval & Parts Sourcing
After our technicians complete a thorough disassembly, our repair planner is able to get a full scope of the damage, including damage that was previously hidden and unable to be documented on the preliminary estimate. We can then finalize our repair plan and assist in submitting a “supplement” to the responsible insurance company informing them of the need for additional operations necessary to complete a proper and safe repair. This process has some variance from company to company; however, a supplement is usually reviewed within 48 hours. After the supplement has been approved, additional parts needed for the repair are ordered. Once received, the parts are inspected for proper fit and function.
Step 7 Frame & Body Repairs
Once all safety inspections and repair procedures have been researched, frame and body repairs can begin. If the vehicle requires frame or unibody straightening, it will head to a dedicated frame bench to be set up and measured with one of our state-of-the-art 3-dimensional measuring systems. After the vehicle has been returned to factory specification, it will transition to the body repair department to have any necessary panel repairs or replacements.
Step 8 Vehicle Refinishing
At this stage, the vehicle is taken to our paint department. All surfaces that were repaired are sanded to proper smoothness and then sprayed with primer. Parts that were replaced sometimes require a primer as well. After the primer is cured, the areas are sanded again and checked to make sure the repair is straight and void of any imperfections. The vehicle is then finally prepped and masked off in the booth to ensure there is no unwanted overspray. One of the most crucial aspects of the repair process is matching your vehicle's factory color. We have state-of-the-art equipment to make this process fast and to ensure an accurate paint color match. After we have achieved the correct variance for color, the vehicle is moved to the heated paint booth. When paint is applied in the booth, it prevents cross-contamination from particles in the air and gives the perfect temperature to promote adhesion and speed up the remainder of the repair process.
Step 9 Final Assembly
After the refinishing stage is complete and all painted parts are checked for proper color and finish the final assembly can begin. The vehicle is brought back to our disassembly/reassembly area and technicians get to work meticulously putting your vehicle back together one bolt and clip at a time.
Step 10 Recalibration
Once the vehicle is completely reassembled, it is time to ensure that all of the safety and convenience systems are functioning as the manufacturer intended. We do this by aiming and calibrating the radar, sensor, and camera systems that were either removed, replaced, or could have been affected by the collision if required. We use state of the art Bosch camera, targeting, and scanning equipment to ensure that all systems are working properly. We then perform a post-calibration test to verify that all functions are working normally.
Step 11 Post Repair Scan & Final Clean
If the vehicle required ADAS system re-calibrations, the vehicle will have been post-scanned at that time. If not, the vehicle will be post-repair scanned using a tool called an asTech device. This allows us to perform a factory-level diagnostic scan on your vehicle ensuring that all systems are working properly and any and all DTC’s that may have been generated during the repair process are cleared. We then take a vehicle on a test drive to ensure that all systems work properly and the vehicle drives as the manufacturer intended. We then wash the vehicle's exterior, vacuum, and wipe down the interior to ensure that it is cleaner than when you left it with us.
Step 12 Quality Assurance & Final Walk Around
After the vehicle has been post-repair scanned, test-driven, and cleaned, it will be inspected by the shop manager and your repair planner. They will ensure that the repairs meet our quality standards and that all items—whether claim-related or customer-pay items—are addressed. Once you come to pick up your vehicle you will then be walked around by your repair planner. They will inform you of all repair work performed and ensure that your expectations are met. Our goal is 100% satisfaction, and if there is ever anything that we could have done better we ask that you notify your repair planner so that it can be corrected.
OUR PROMISE IS OUR GUARANTEE
Frank and Sons Auto Body puts safety, quality, and service above all else. We promise to strive for the highest level of quality and safe repair in the most efficient manner possible. We will work hard to return your vehicle as quickly as possible without sacrificing our commitment to craftsmanship or safety of your vehicle. Frank and Sons Auto Body prides itself on our quality control processes and provides a lifetime warranty on all work performed for as long as you own your vehicle.
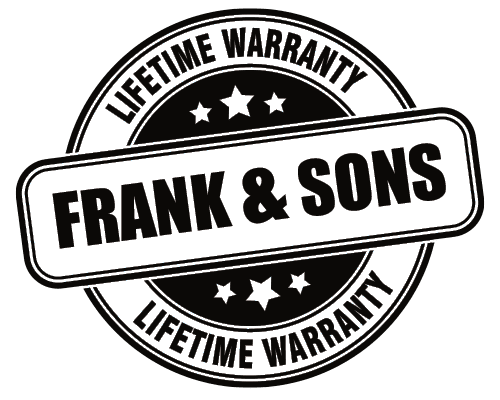